Drying production line
Message
Description
To obtain high quality mixtures, all the initial components of the mixture must be dry. The moisture content of the sand should be no higher than 0.5%. For sand drying, three cylinder drum dryer or conventional dryer are used. After drying, Feeding dry sand to vibrating screens with 1, 2 or 3 layers screen (usually with a mesh size of 0.63, 1.2 and 2.0mm respectively) for classification. After classification, the sand will be conveyed to bunkers for cooling to the required temperature, after which each size sand will be fed to the weighing unit, then mixing and packaging.
The sand drying productin line for drying sand is used for wet sand or other bulk material drying. The dry sand is widly used in the production of dry building mixtures.
The drying production line is a complete set of equipment for heat drying and screening sand or other bulk materials. It consists of the following parts: wet sand hopper, belt feeder, belt conveyor, burning chamber, rotary dryer (three-cylinder dryer, single-cylinder dryer), cyclone, pulse dust collector, draught fan, vibrating screen, and electronic control system.
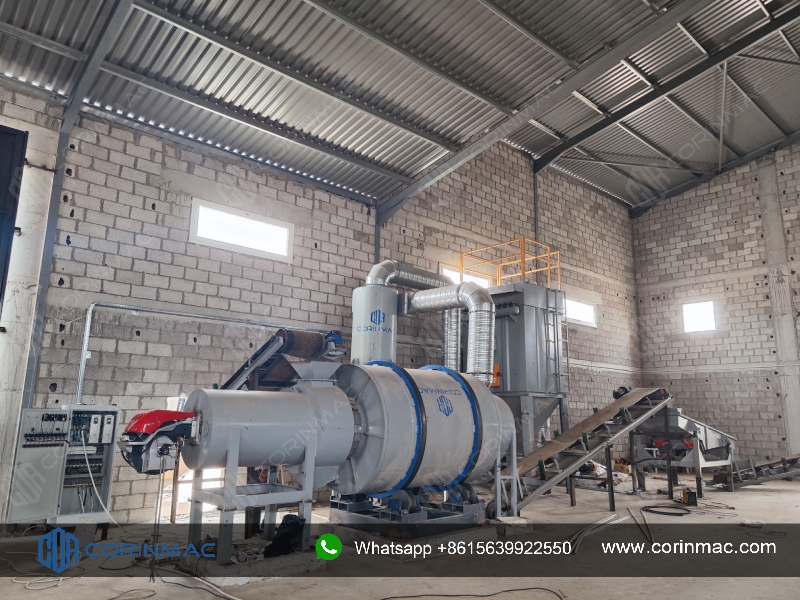
The drying production line is a complete set of equipment for heat drying and screening sand or other bulk materials. It consists of the following parts: wet sand hopper, belt feeder, belt conveyor, burning chamber, rotary dryer (three-cylinder dryer, single-cylinder dryer), cyclone, pulse dust collector, draught fan, vibrating screen, and electronic control system.
Wet sand hopper
The wet sand hopper is used to receive and store the wet sand to be dried. The volume (standard capacity is 5T) can be customized according to user needs. The outlet at the bottom of the sand hopper is connected to a belt feeder. The structure is compact and reasonable, strong and durable.
![]() |
![]() |
Belt feeder
The belt feeder is the key equipment for evenly feeding the wet sand into the dryer, and the drying effect can be guaranteed only by feeding the material evenly. The feeder is equipped with a variable frequency speed regulating motor, and the feeding speed can be adjusted arbitrarily to achieve the best drying effect. It adopts skirt conveyor belt to prevent material leakage.
![]() |
![]() |
Belt conveyor
Belt conveyor is used to send the wet sand to the dryer, and convey the dried sand to the vibrating screen or any designated position. We use nylon conveyor belt, which has high strength, impact resistance and long life.
![]() |
![]() |
Burner
Depending on the user's fuel, we can provide gas burners, light oil burners, heavy oil burners, pulverized coal burners, and biomass pellet burner, etc.
![]() |
![]() |
Burning chamber
Provide space for fuel combustion, the end of the chamber is provided with an air inlet and an air regulating valve, and the interior is built with refractory cement and bricks, and the temperature in the burning chamber can reach up to 1200 ℃. Its structure is exquisite and reasonable, and it is closely combined with the dryer cylinder to provide sufficient heat source for the dryer.
![]() |
![]() |
Three cylinder rotary dryer
The three cylinder rotary dryer is an efficient and energy-saving product improved on the basis of the single-cylinder rotary dryer.
There is a three-layer drum structure in the cylinder, which can make the material reciprocate three times in the cylinder, so that it can obtain sufficient heat exchange, greatly improve the heat utilization rate and reduce power consumption.
![]() |
![]() |
Cyclone
It is connected to the air outlet of the dryer end cover through a pipeline, and is also the first dust removal device for the hot flue gas inside the dryer. There are a variety of structures such as single cyclone and double cyclone group could be chosen.
![]() |
![]() |
Impulse dust collector
It is another dust removal equipment in the drying line. Its internal multi-group filter bag structure and pulse jet design can effectively filter and collect dust in the dust-laden air, so that the dust content of the exhaust air is less than 50mg/m³, ensuring that it meets the environmental protection requirements. According to the needs, we have dozens of models such as DMC32, DMC64, DMC112 for selection.
![]() |
![]() |
Draught fan
The draught fan is connected to the impulse dust collector, which is used to extract the hot flue gas in the dryer, and it is also the power source for the gas flow of the entire drying line.
![]() |
![]() |
Vibrating screen
After drying, the finished sand (water content is generally below 0.5%) enters the vibrating screen, which can be sieved into different particle sizes and discharged from the respective discharge ports according to the requirements. Usually, the size of the screen mesh is 0.63mm, 1.2mm and 2.0mm, the specific mesh size is selected and determined according to actual needs.
![]() |
![]() |
All steel screen frame, unique screen reinforcement technology, easy to replace the screen.
![]() |
![]() |
Contains rubber elastic balls, which can automatically clear the screen blockage.
![]() |
![]() |
Multiple reinforcing ribs, more robust and reliable.
Electronic control system
The entire production line is controlled in an integrated manner, with a visual operation interface, through frequency conversion to adjust the speed of the feed and drying drum rotates, intelligently control the burner, and realize intelligent temperature control and other functions.
![]() |
![]() |
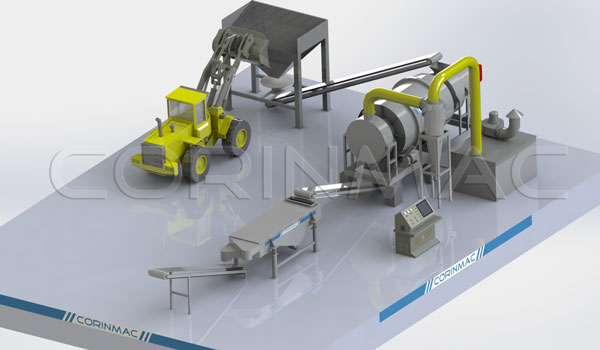
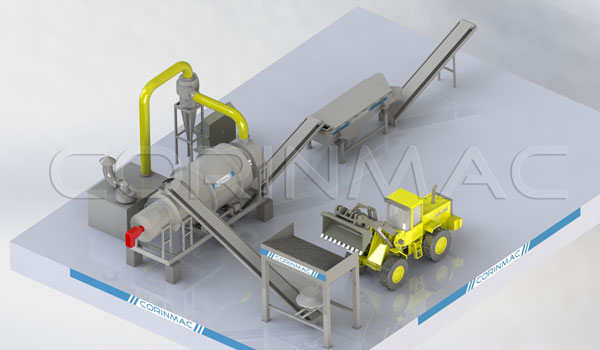
Specification
Equipment list | Capacity(Original moisture 5-8%) | |||||
3-5tph | 8-10 tph | 10-15 tph | 20-25 tph | 25-30 tph | 40-50 tph | |
Wet sand hopper volume | 5t | 5 t | 5 t | 10 t | 10 t | 10 t |
Belt feeder | PG500 | PG500 | PG500 | PG500 | PG500 | PG500 |
Belt conveyor | В500х6 | В500х8 | В500х8 | В500х10 | В500х10 | В500х15 |
Three-circuit drum dryer | CRH6205 | CRH6210 | CRH6215 | CRH6220 | CRH6230 | CRH6250 |
Burning chamber | Matched(with refractory brick) | |||||
Burner (gas/diesel) Thermal power |
RS/RL 44T.C 450-600kw |
RS/RL 130T.C 1000-1500 kw |
RS/RL 190T.C 1500-2400 kw |
RS/RL 250T.C 2500-2800 kw |
RS/RL 310T.C 2800-3500 kw |
RS/RL 510T.C 4500-5500 kw |
Belt conveyor | В500х6 | В500х6 | В500х6 | В500х8 | В500х10 | В500х10 |
Vibrating screen(According to sand size) | DZS1025 | DZS1230 | DZS1230 | DZS1540 | DZS1230(2sets) | DZS1530(2sets) |
Belt conveyor | В500х6 | В500х6 | В500х6 | В500х6 | В500х6 | В500х6 |
Cyclone | Φ500mm | Φ1200 mm | Φ1200 mm | Φ1200 | Φ1400 | Φ1400 |
Draught fan |
Y5-47-5C (5.5кw) |
Y5-47-5C (7.5кw) |
Y5-48-5C (11кw) |
Y5-48-5C (15кw) |
Y5-48-6.3C 30кВт |
Y5-48-6.3C 45кВт |
Pulse dust collector | MC-80 | MC-32-4 | MC-32-6 | MC-64-4 | MC-64-6 | MC-96-6 |
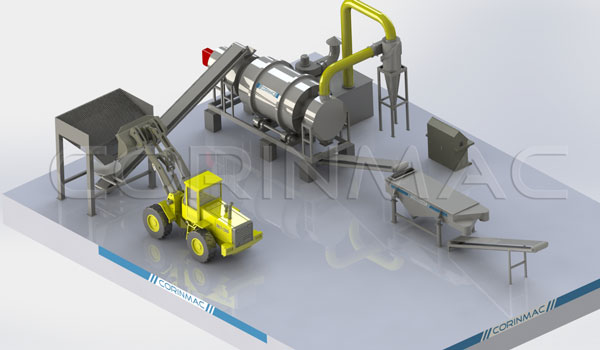
1 to 1 customized service
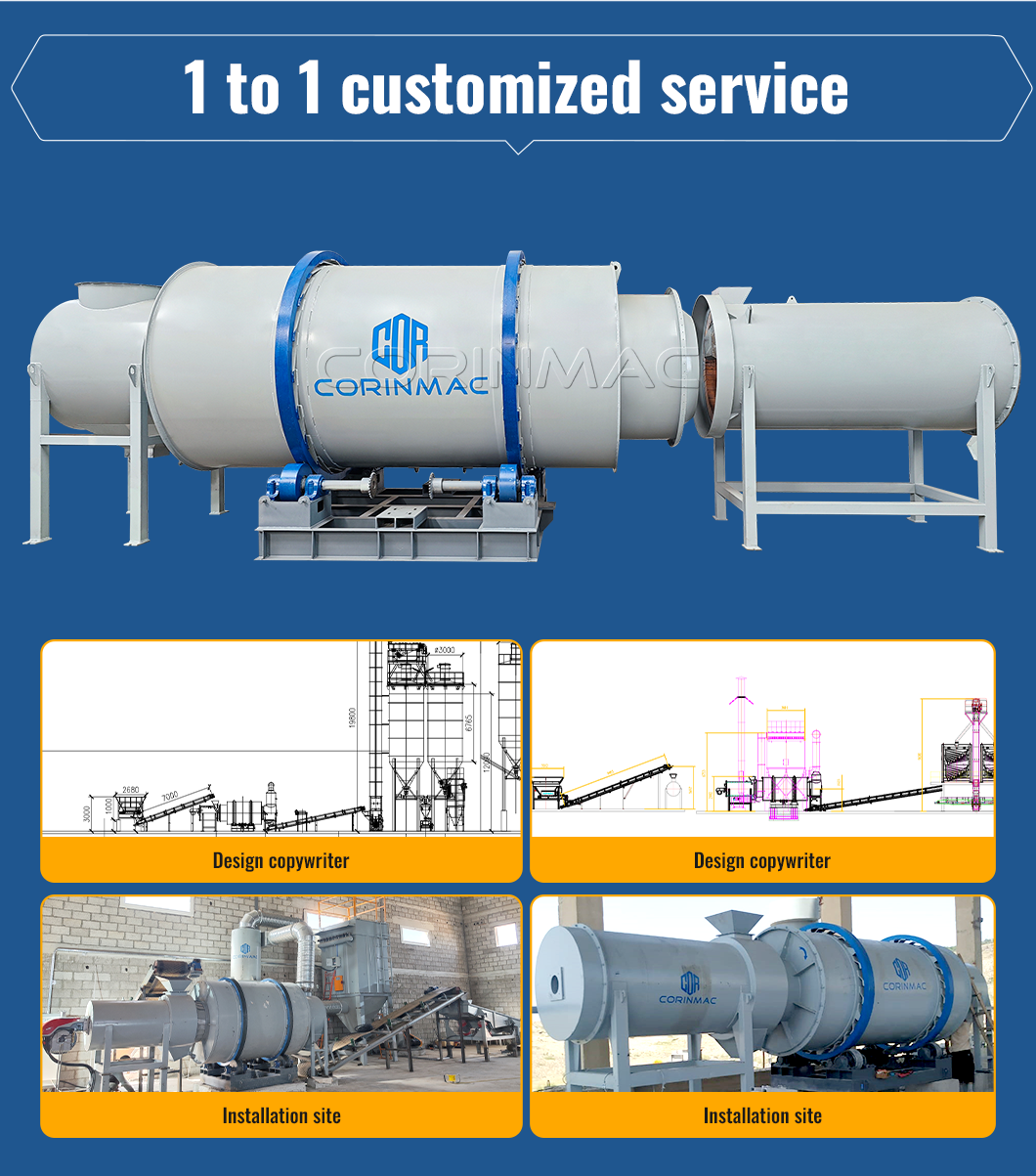
Scope of application:
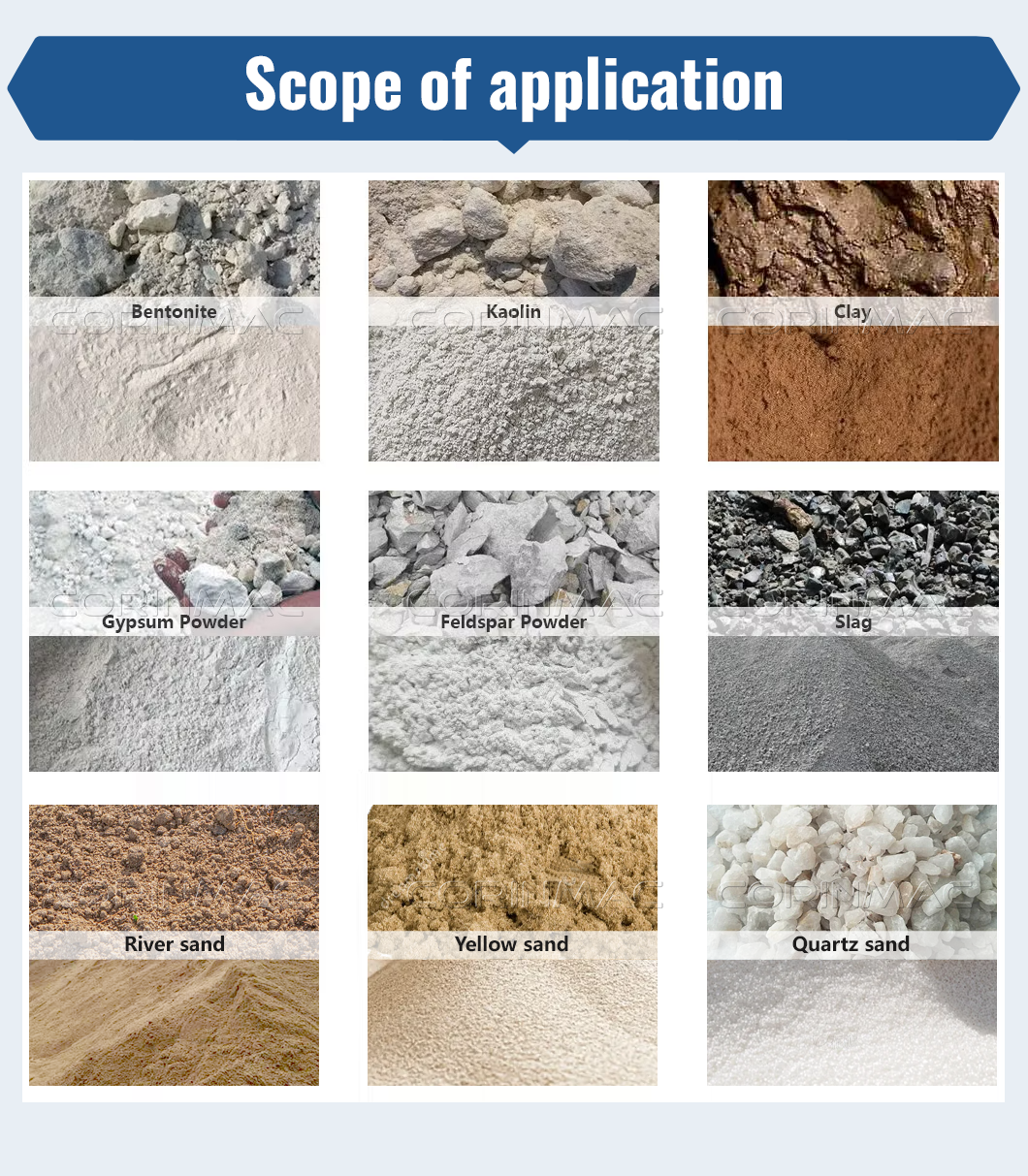
Successful Project
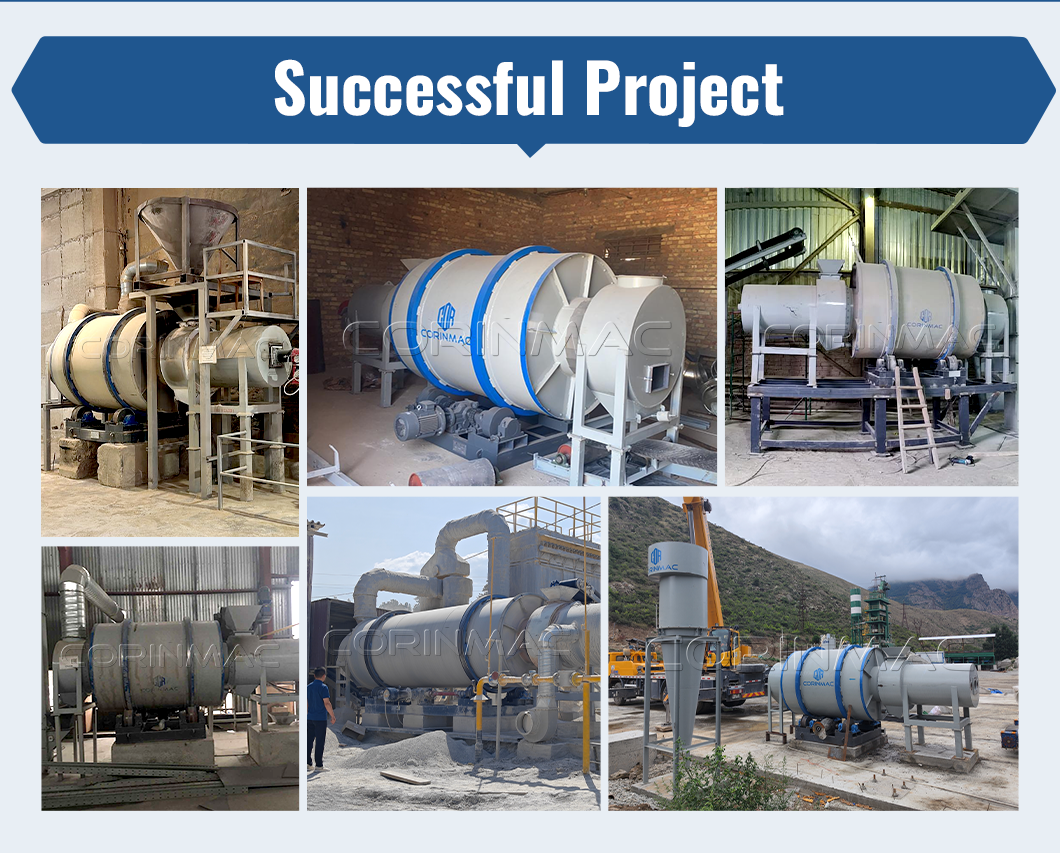
Company Profile
CORINMAC-Cooperation& Win-Win, this is the origin of our team name.
This is also our operating principle: through teamwork and cooperation with customers, create value for individuals and customers, and then realize the value of our company.
Since its founding in 2006, CORINMAC has been a pragmatic and efficient company. We are committed to finding the best solutions for our customers by providing high-quality equipment and high-level production lines to help customers achieve growth and breakthroughs, because we deeply understand that customer's success is our success!
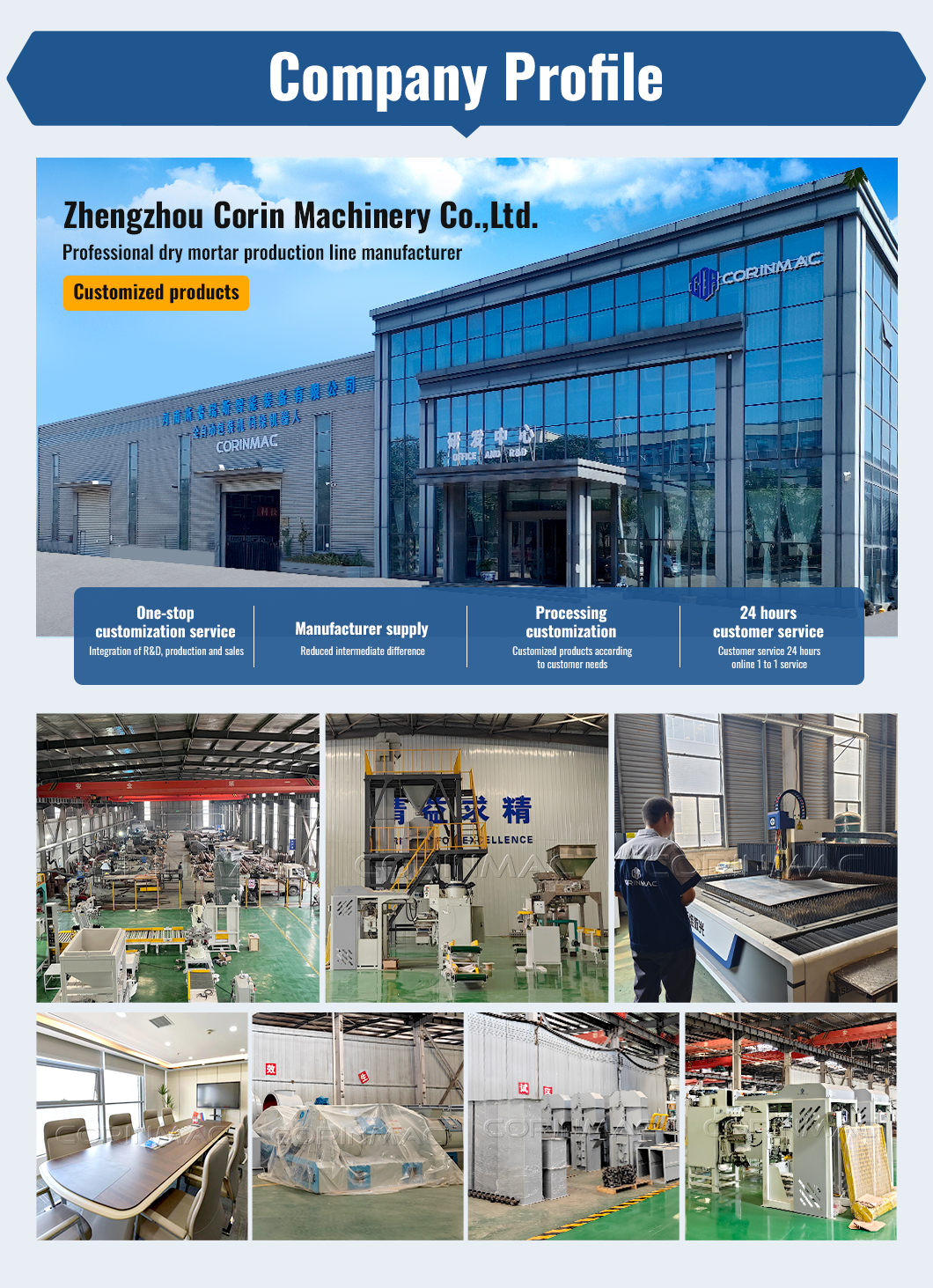
Customer visits
Welcome to CORINMAC. CORINMAC's professional team offers you comprehensive services. No matter which country you come from, we can provide you with the most considerate support. We have extensive experience in dry mortar manufacturing plants. We will share our experience with our customers and help them start their own business and make money. We thank our customers for their trust and support!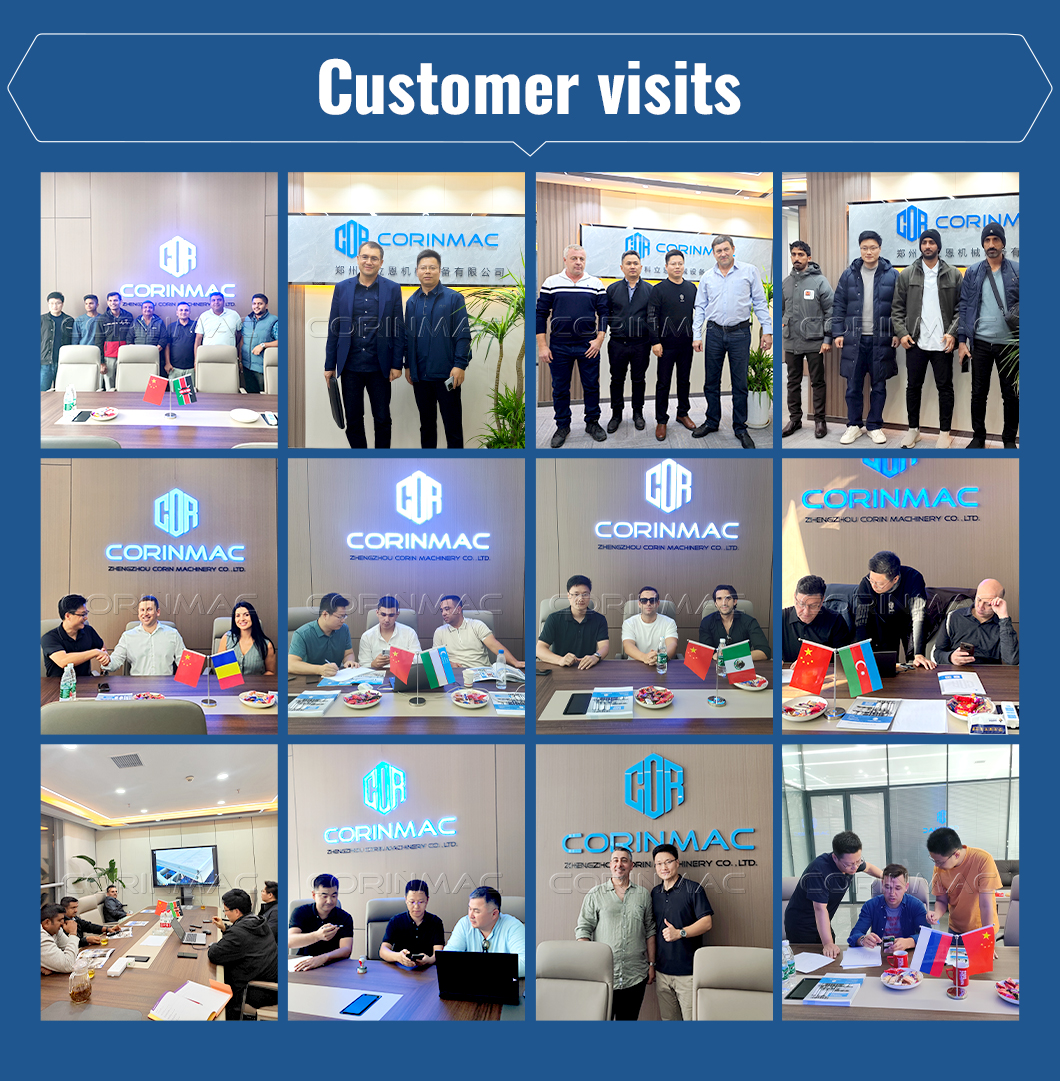
Packaging for shipment
CORINMAC has professional logistics and transportation partners who have cooperated for more than 10 years, providing door-to-door equipment delivery services.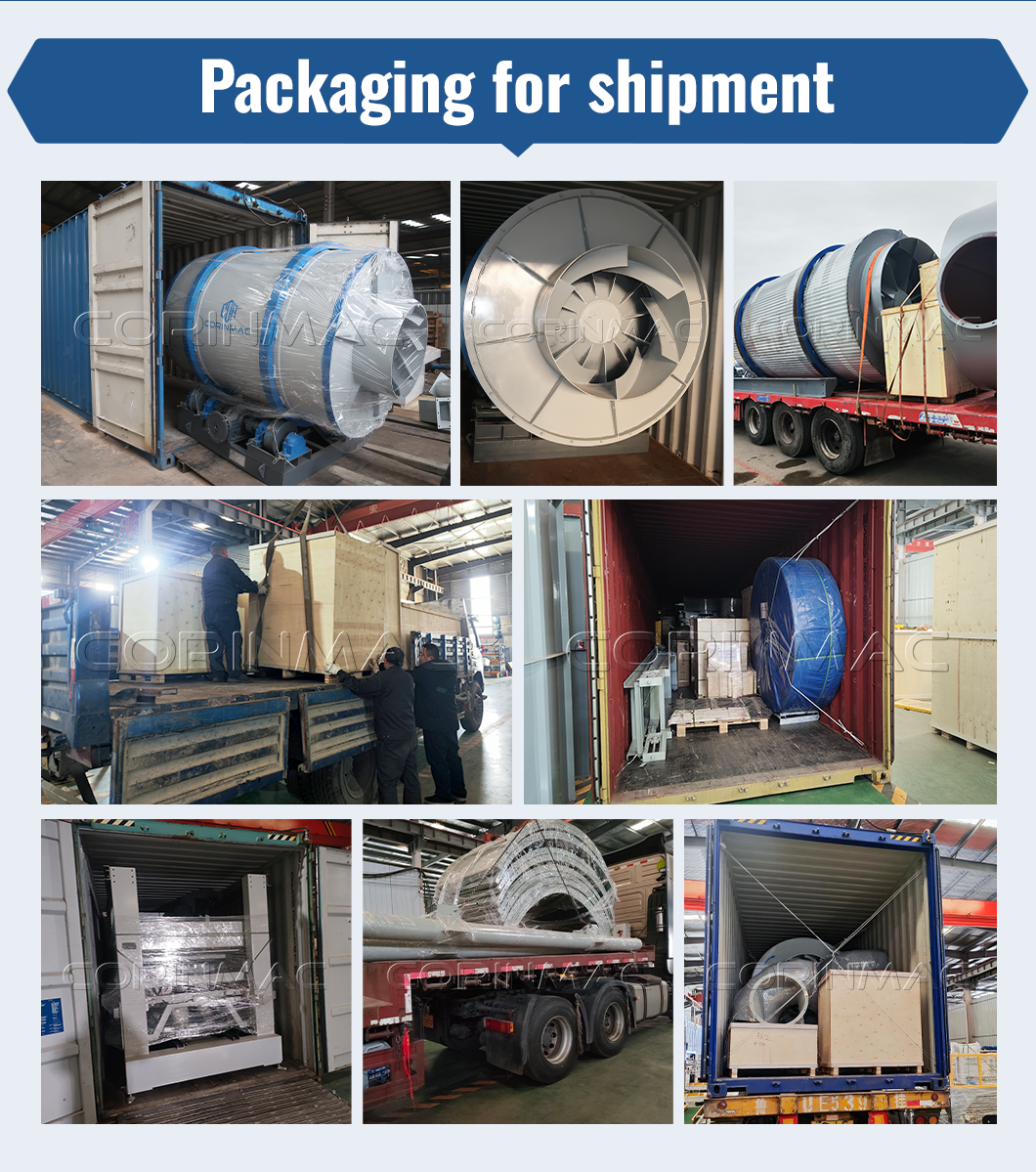
Customer feedback
Our products have won a good reputation and recognition in more than 40 countries, including the United States, Russia, Kazakhstan, Kyrgyzstan, Uzbekistan, Turkmenistan, Mongolia, Vietnam, Malaysia, Saudi Arabia, the United Arab Emirates, Qatar, Peru, Chile, Kenya, Libya, Guinea, Tunisia, etc.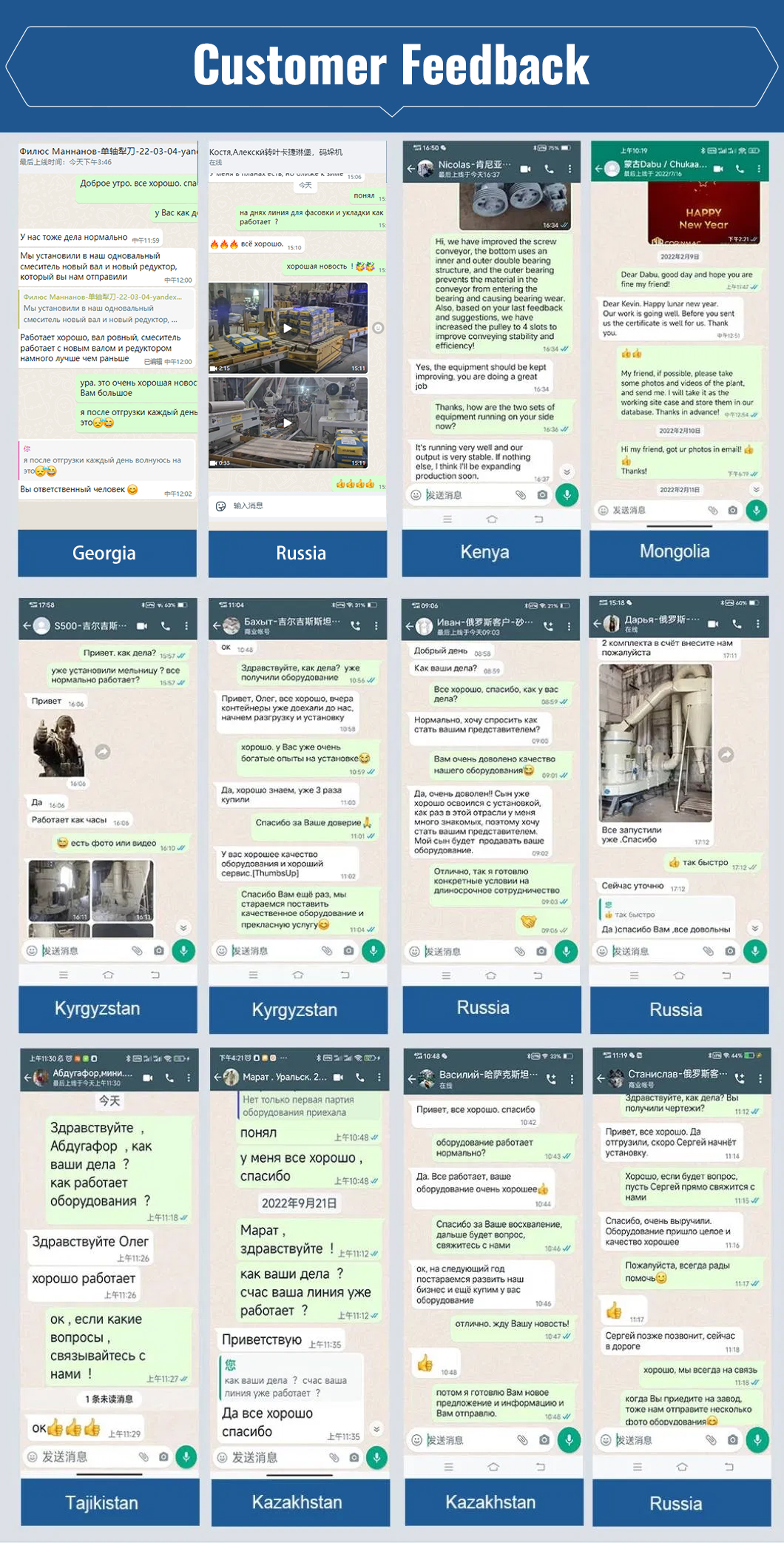